DIGITAL TWIN DLA CIĄGŁEJ POPRAWY PRODUKCJI
„Koncepcja Cyfrowego Bliźniaka Asseco CEIT, oparta na Sewio RTLS, otworzyła przed nami całą gamę przypadków użycia, które nieustannie realizujemy, z każdym krokiem osiągając wyższy poziom dojrzałości cyfrowej, zwiększając wydajność i co najważniejsze, uzyskując przewagę konkurencyjną. Łączy sytuacje w czasie rzeczywistym ze środowiskiem cyfrowego bliźniaka, w którym możemy podejmować natychmiastowe działania naprawcze i pozyskiwać solidną bazę danych do analizy. Nie możemy zmienić tego, co wydarzyło się dzisiaj, ale możemy analizować, uczyć się i wpływać na to, co wydarzy się jutro z pomocą kompetencji Asseco CEIT.”
Rastislav Ruckay
Production Improvement Manager, VELUX Commercial
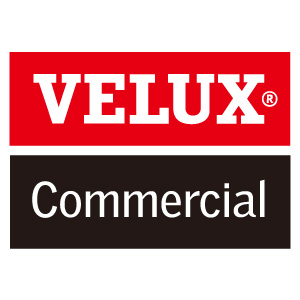
Przemysł: Windows and skylights manufacturing
Lokalizacja: Manufacturing facility, Østbirk, Denmark
Asseco CEIT rozwiązanie: System AGV, Twiserion Design Manager, Twiserion Digital Manager, symulacja dynamiczna, skanowanie laserowe 3D i digitalizacja obiektów
Transformacja w kierunku innowacyjnej produkcji
Firma VELUX Commercial zdecydowała się przekształcić ręczny system produkcji nowego produktu – modułowych świetlików dachowych VELUX – w innowacyjny, półautomatyczny i w pełni zautomatyzowany system o potencjale modułowości i wyższej wydajności, ponieważ oferuje on wysoce spersonalizowane produkty. Aby umożliwić w pełni ciągłe doskonalenie, koncepcja cyfrowego bliźniaka musiała zostać wdrożona ze wszystkimi systemami połączonymi ze sobą, aby przynieść wszystkie korzyści.
Droga do ciągłego doskonalenia
Asseco CEIT najpierw zaprojektowało koncepcyjny układ linii produkcyjnej opartej na pojazdach AGV jako wysoce efektywny ze względu na zapewnienie maksymalnej elastyczności procesu montażu i przedstawiło go za pomocą wizualizacji VR. Szczegółowa symulacja dynamiczna dostarczyła informacji na temat wymaganej liczby pojazdów AGV, które należy wdrożyć w celu realizacji prognozowanej przyszłej produkcji mieszanej.
Zainstalowano pojazdy AGV ze specjalnymi chwytakami, a cały system sterowania został podłączony do produkcyjnego systemu SAP. Następnie skonfigurowano sieć RTLS opartą na UWB z wykorzystaniem 40 tagów osobistych, 17 tagów AGV i dwóch ręcznych wózków widłowych, które komunikują się z 12 kotwicami i obejmują obszar 2 304 m². Dodano funkcje, takie jak lokalizacja, powiadamianie operatorów, automatyczna regulacja wysokości chwytaka w celu uzyskania optymalnej ergonomii, planowanie oraz kontrolowanie i monitorowanie TPM.
Zautomatyzowane stanowiska produkcyjne zostały podłączone do wszystkich wewnętrznych systemów, a cyfrowy bliźniak został stworzony z pulpitami VR. Jednym z ostatnich kroków była optymalizacja codziennego procesu planowania produkcji przeprowadzona przy użyciu dynamicznej symulacji, a także rzeczywistych danych z prawdziwego systemu produkcyjnego w cyfrowym bliźniaku.
Projekt w liczbach:
Zwiększone bezpieczeństwo
przegląd świadomości i zrozumienie poprzez szkolenie w zakresie bezpieczeństwa
3x
Zwiększona wielkość produkcji przy tej samej przestrzeni
40%
wzrost produktywności dzięki lepszemu zarządzaniu halą produkcyjną i automatyzacji produkcji
50%
zwiększenie wydajności działań TPM
10%
Zmniejszenie WIP dzięki ulepszonym kanałom komunikacji
70%
skrócenie czasu procesu planowania optymalnej sekwencji produkcji dzięki wykorzystaniu danych rzeczywistych i dynamicznej symulacji
Korzyści z projektu
-
- Zwinny system produkcyjny zdolny do efektywnego reagowania na wymaganą wielkość produkcji przy jednoczesnym oszczędzaniu mocy produkcyjnych i kosztów
- Zgromadzone i ocenione dane wykorzystywane do obliczania KPI w czasie rzeczywistym dla pulpitów nawigacyjnych i różnych raportów
- Przywrócenie nastawienia z działań reaktywnych na proaktywne
- Rozwój ludzi i organizacji poprzez zaangażowanie członków zespołu w proces transformacji – nauka nowych umiejętności, przekształcenie obowiązków zawodowych
- Stworzono bazę danych opartą na wiedzy do dalszego wykorzystania, co ma kluczowe znaczenie dla utrzymania wysokiego poziomu standaryzacji procesów
- Digitalizacja w produkcji – przekształcenie papierowego środowiska produkcyjnego w zdigitalizowany proces połączony z cyfrowym bliźniakiem
.