PETER MAČUŠ: Es ist einfach. „Innovieren“ bedeutet „überleben“ in der Industrie
Vor mehr als zehn Jahren war er bei der Geburt unbeaufsichtigter Robotertraktoren, die lange Zeit zu einer Art Flaggschiff der technischen Innovationen von Asseco CEIT wurden und es zu einem der wichtigsten slowakischen Akteure auf dem Gebiet der Modernisierung von Industrieanlagen machten. Peter Mačuš, technischer Direktor von Asseco CEIT, erklärt, dass gelbe LKWs für den automatisierten Materialtransport heute nur noch eins der Komponenten eines mobilen Robotersystems sind, das sich allmählich zu einer umfassenden intelligenten Logistiklösung entwickelt hat. Eine solche Logistik ist wiederum ein wichtiger Bestandteil der gesamten intelligenten Anlage. Als der richtige Partner für industrielle Innovation baut Asseco CEIT ein eigenes Konzept für intelligente Fabriken auf. Gleichzeitig bauen wir auf soliden Grundlagen auf, da wie neben den genannten technischen Innovationen und der Automatisierung auch Vorreiter bei den Werkzeugen des digitalen Unternehmens und führend bei Optimierungen verschiedener Art sind. Wie sieht ein so intelligentes Unternehmen nach Asseco CEITs Verständnis aus? Warum ist es für eine Industrieanlage wichtig, eine intelligente Anlage zu werden? Warum sollte es ständig innovativ sein und auf den technologischen Fortschritt reagieren? Laut Petr Mačuš ist die Antwort sehr einfach. Innovation sei eine notwendige Voraussetzung für das „Überleben“ angesichts des starken Wettbewerbs.
Wenn dieses Interview vor einem Jahr stattgefunden hätte, hätten wir mit einer Industrie 4.0-Frage begonnen. Heute ist es jedoch so, als ob das Konzept zurückgegangen wäre oder als hätte es seinen Schwung verloren. Einige nannten es sogar eher eine Modewelle als eine echte industrielle Revolution. Stimmen Sie zu? Ist es altmodisch Industrie 4.0 einzusetzen?
Ich würde sagen, dass der Begriff „Industry 4.0“ oder in der deutschen Version „Industrie 4.0“ so massiv mitschwang, dass wir damit in gewissem Maße übersättigt sind. Es wurde viel darüber diskutiert, viele wollten „Industrie 4.0 sein“ oder, wie Sie sagten, Industrie 4.0 „bereitstellen“, oft ohne, dass klar war, worum es genau ging. Wir bei Asseco CEIT haben dieses Konzept noch nie als ein Abzeichen gesehen, das erhältlich ist, oder als eine Zielstation, die erreicht werden kann, wenn das Unternehmen die genauen Bedingungen erfüllt. Haben Sie eine automatisierte Logistik? Sammeln Sie Daten? Alles klar, fertig, Sie sind bereits Industrie 4.0. So denken wir nicht, dass es funktioniert. Man kann den Weg der Industrie 4.0 gehen.
Dies bedeutet, ständig auf den technologischen Fortschritt zu reagieren. Streben Sie nach Innovation. Einführung neuer und neuer Technologien und Praktiken. Es ist unbestreitbar, dass sich die rasante technologische Entwicklung radikal verändert hat und das Gesicht der Industrie weiter verändert. Nur wer diese Entwicklung nicht ignoriert, kann Erfolg haben, im Gegenteil, sie reagieren umgehend darauf und interessieren sich sehr dafür. Sie wissen, dass dies unerlässlich ist, um die Produktivität und Leistung ständig zu steigern, den wachsenden Wettbewerb voranzutreiben, weiterzuentwickeln und zu überstehen. Industrieunternehmen müssen nach digitalen Geschäftstools, Automatisierung oder künstlicher Intelligenz greifen. Bei Asseco CEIT entwickeln wir diese Themen seit Jahrzehnten. Es wurde also nur bestätigt, dass die Lösungen, die wir Industrieunternehmen anbieten, wirklich fortschrittlich sind und manchmal ihrer Zeit voraus sind. Das ist schließlich unsere Aufgabe. Als richtiger Innovationspartner müssen wir mindestens einen Schritt voraus sein.
Man kann also sagen, dass die Welle intensiver Debatten über Industrie 4.0 die Bedeutung neuer Technologien unterstrichen hat?
Genau. Wie auch immer wir es nennen, der gerade erwähnte technologische Fortschritt und die Notwendigkeit, darauf zu reagieren, sind in den Vordergrund gerückt. Heute zweifelt niemand daran, dass dies der Schlüssel für ihre Bemühungen zur Steigerung der Produktivität ist. Denn darum geht es immer. Seien Sie produktiv und effizient. Industrieunternehmen denken pragmatisch. Sie würden kaum neue Technologien einführen, nur weil es „in“ ist. Zunächst fragen sie: Was bringt es uns, was werden wir gewinnen? Sie brauchen klare Antworten auf diese Fragen.
Deshalb hat Asseco CEIT ein eigenes Konzept für intelligente Fabriken entwickelt?
Wie bereits erwähnt, möchten wir ein verlässlicher Innovationspartner für die Industrie sein. Als sich die Debatten über die industrielle Revolution oder Industrie 4.0 auch in der Slowakei zu intensivieren begannen, brachten sie gleichzeitig viele Fragen und Unklarheiten mit sich. Viele fragten, was sollen wir tun? Was ist zu tun? Es war unsere Aufgabe, eine Antwort zu geben. Denn dies waren die Themen, in denen wir zu Hause waren, sei es ein digitales Unternehmen, Robotik, Automatisierung, Prozessinnovation, virtuelle und erweiterte Realität, fortschrittliche Datenerfassung und -verarbeitung.
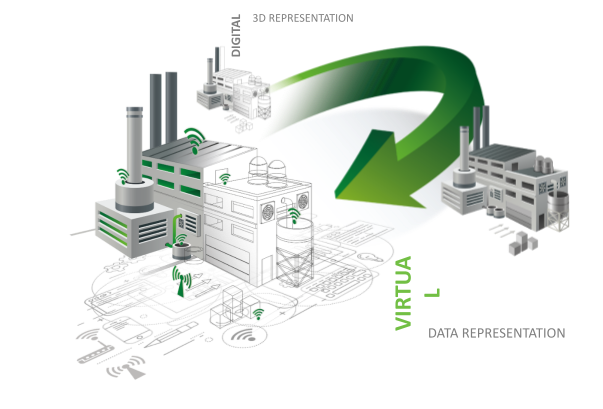
Basierend auf den Ideen eines der Gründer unserer Gesellschaft, eines anerkannten Experten und Visionärs, Professor Milan Gregor, ist unser Konzept intelligenter Fabriken eine Kombination aus drei Welten: digital, real und virtuell. Es folgt eine umfassende Digital Twin-Lösung, mit der schrittweise und systematisch ein modernes Geschäftsumfeld im Sinne von Industrie 4.0 aufgebaut werden kann. Digital Twin, eigentlich ein Synonym für das intelligente Unternehmen der Zukunft, repräsentiert nach unserem Verständnis einen komplexen Zyklus von der Digitalisierung über die Implementierung selbst bis hin zur autonomen Steuerung und Selbstoptimierung. (Der Factory Twin-Produkthinweis ist Digital Twin & Factory Twin auf Seite 7-14 gewidmet.)
Für jede dieser Phasen bietet Asseco CEIT eine Reihe spezifischer Lösungen. Wenn Sie erwähnt haben, dass Industrieanlagen sie immer hauptsächlich aus der Perspektive des Pragmatismus betrachten, was kann Digital Twin in dieser Hinsicht bringen?
Zunächst muss gesagt werden, dass jedes Industrieunternehmen individuell angesprochen werden muss, abhängig von der Art und dem Volumen der Produktion, dem Automatisierungsgrad oder dem Standardisierungsgrad der Prozesse, einer Reihe anderer Faktoren, von denen ich Dutzende nennen könnte.
Digital Twin ist eine Erweiterung eines digitalen Unternehmens. Wenn wir nur dieses Konzept entwickeln, bringen die Werkzeuge eines digitalen Unternehmens Industrieanlagen enorme Vorteile. Dank einer Reihe moderner Technologien ist es möglich, digitale Modelle aller Elemente eines Unternehmens zu erstellen, sei es Teile, Produkte, Technologien, Fertigungsprozesse, Menschen oder Managementsysteme. Wenn ein Unternehmen über ein digitales Modell verfügt, können Änderungen einfacher, schneller und vor allem effizienter geplant werden. Dynamische Simulations- und 3D-Visualisierungstools helfen dann bei der Feinabstimmung aller Details. Als Beispiel möchte ich die interaktive Twiserion Design Manager erwähnen, die ein hervorragender Helfer bei der Erstellung neuer Produktions- oder Logistikkonzepte ist. Sie müssen lediglich das Layout auf dem Touchpanel ändern und das System bewertet sofort die Vor- und Nachteile. VORTEILE? Auch dies spart Zeit und Geld. Viele Industrieanlagen (nicht nur) in der Slowakei haben Erfahrung mit digitalen Unternehmenstools, ihre Bedeutung muss wahrscheinlich nicht betont werden. Wir sind jedoch noch weiter gegangen und haben diese digitale Welt mit einer virtuellen Umgebung erweitert. Die von den allgegenwärtigen Sensoren erhaltenen Daten erzeugen ein tatsächliches Bild der realen Umgebung, das für die weitere Optimierung wichtig ist.
Viele Industrieunternehmen stehen vor der Frage, wie sie mit Daten arbeiten sollten.
Der Mehrwert dieser Daten ist enorm. Erfassung, Überwachung und Visualisierung ist nur der erste Schritt, gefolgt von der Analyse von Fakten und Statistiken. Wenn wir uns einer Echtzeitreaktion zuwenden, sprechen wir bereits von autonomem Management. Darauf folgt die Fähigkeit, Probleme vorherzusagen, d.h. automatisch zu verhindern. Durch den Einsatz künstlicher Intelligenz gelangen wir in die Phase der Selbstoptimierung, Selbstorganisation und Rekonfigurierbarkeit, die unseres Erachtens das Thema der kommenden Jahre ist.
Welche Pläne hat Asseco CEIT in dieser Hinsicht?
Bei der Entwicklung des Digital Twin-Konzepts hat CEIT eine erfolgreiche Zusammenarbeit mit Sewio aufgebaut, insbesondere im Bereich RTLS (Real Time Location System). Ich kann sagen, dass Asseco CEIT bereits spezielle hochentwickelte Sensorsysteme vorbereitet, um Daten aus den Teilen des Produktionssystems zu sammeln, in denen dies heute noch nicht möglich ist. Dies ist jedoch eine notwendige Voraussetzung für ein autonomes Management.
Wir haben die digitale Welt und die virtuelle Welt erwähnt. Ihr gemeinsamer Schnittpunkt ist die reale Welt. Trotz des technologischen Fortschritts spielen die Menschen immer noch eine wichtige Rolle. Zählt der Digital Twin auf Leute?
Ja, sicher. Es ist jedoch klar, und ich werde nichts Neues sagen, dass die Industrie Menschen braucht, die bereit sind, mit fortschrittlichen Technologien zu arbeiten, Menschen, die bereit und vor allem willig sind, mit dem sich ändernden industriellen Umfeld umzugehen. Die Vorbereitung selbst kann auf moderne, innovative Weise unter Verwendung von virtueller oder erweiterter Realität erfolgen. Zu diesem Zweck kann beispielsweise ein virtueller Simulator verwendet werden, der die Entwicklung der Fähigkeiten und Kompetenzen der Mitarbeiter in einer ursprünglichen Erfahrungsform ermöglicht.
Digital Twin ist ein komplexes und sehr umfassendes Konzept. Können Sie ein konkretes Beispiel für den praktischen Einsatz geben?
Ich stimme zu, dies ist eine komplexe und sehr ausgefeilte Lösung, die auf Teilstufen aufgebaut ist, von denen jede wichtig ist. Digital Twin ist eine Antwort nicht nur auf die aktuelle, sondern auch auf die erwartete technologische Entwicklung und ein einzigartiger „Made in Slovakia“ – Ansatz. Bei der Entwicklung dieses Konzepts berücksichtigen wir erneut nicht nur aktuelle Trends, sondern blicken auch in die Zukunft. Für die reale Industriepraxis ist die Digital Twin-Version für rekonfigurierbare Logistik vielleicht das beste Beispiel. Schließlich hat unser im größten Automobilwerk der Slowakei implementiertes intelligentes Logistiksystem kürzlich die renommierten European Automotive Logistics Awards gewonnen, auf die wir sehr stolz sind. Gleichzeitig ist es für uns eine Herausforderung, unseren eigenen Ansatz zur revolutionären Transformation der heutigen Produktion weiterzuentwickeln.