Benefits of using AGV forklifts in handling in production and logistics
Date: 4. september 2024, Author: Peter Ščerba, Ladislav Ruttkay
Automation in industry is constantly evolving, bringing new technologies that improve the efficiency and safety of operations. One of the innovative and already established solutions is the Automated Guided Vehicle (AGV). One category of automated equipment is the fork-lift AGV. These trucks are designed to perform material handling and transport with minimal human intervention, while retaining all the advantages of standard forklift technology, thus offering many benefits in logistics and industrial environments.
Efficiency and productivity
One of the biggest advantages of using AGV forklifts is their ability to work continuously, without the need for breaks. In traditional logistics operations, the human workforce naturally needs breaks, which can lead to a reduction in overall productivity. In contrast, AGVs can work 24/7, allowing operations to run smoothly even during night shifts, weekends or holidays.
Another key advantage is the accuracy and repeatability of operations. AGV forklifts are programmed to perform their tasks with extreme precision, minimizing errors and improving the quality of logistics processes. This factor is particularly important in environments where accuracy and consistency are required, such as assembly lines or warehouses with high goods turnover.
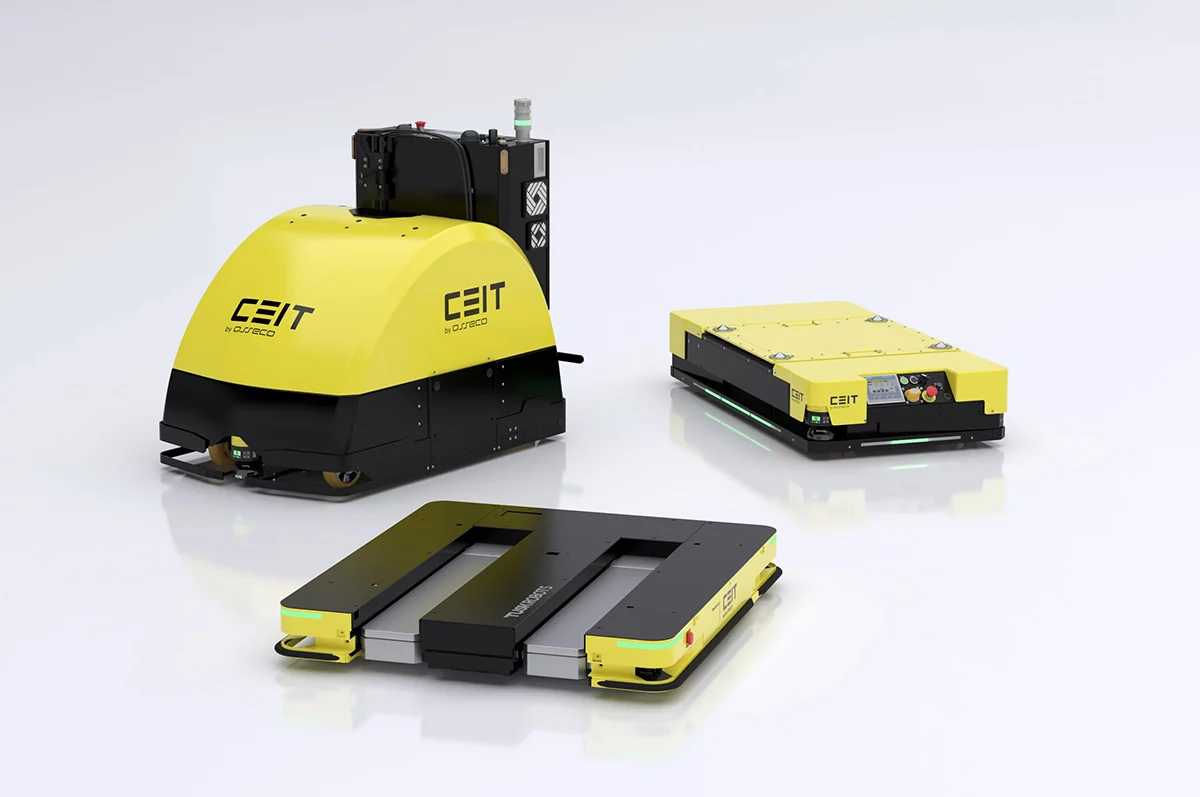
Safety
Safety is one of the most important aspects in any work environment. Traditional human-driven forklifts can be a source of hard-to-predict accidents and injuries. AGVs, however, are equipped with advanced sensors and obstacle detection systems that allow them to safely navigate the environment and avoid collisions. These systems include advanced laser scanners, cameras, and other technologies that monitor the truck’s surroundings, in real time.
The use of AGVs also reduces the risk of employee injuries associated with the manual handling of heavy loads. Automating these tasks reduces the physical strain on workers, leading to a better working environment and reducing the risk of long-term health problems associated with repetitive tasks.
Flexibility and adaptability
Modern AGV systems are extremely flexible and can be adapted to different types of tasks and environments. Forklifts can be used to handle pallets, containers or other large items in a wide range of industries, from manufacturing to distribution.
Their flexibility is also reflected in their ability to adapt to changes in workplace layout. If there is a change in the layout of a warehouse or production lines, AGVs can be quickly reprogrammed to new routes and tasks, minimising downtime and ensuring smooth operations.

Reduction of operating costs
Although the initial investment in an AGV system may be higher compared to traditional trucks, the long-term savings are significant. The use of AGVs reduces the need for manual labour, allowing for more efficient use of manpower. In addition, AGV systems help to reduce the costs associated with handling errors and damage to goods, which are often the result of human error.
Automated trolleys are also energy efficient. They are powered by long-life batteries that require minimal maintenance. The ability to charge automatically without the need to change batteries during the charging process makes the equipment even more economical to use, reducing fuel and maintenance costs.
Improving inventory management and material tracking
In intralogistics, AGVs are used for various purposes. They can be used to transport materials between production lines, distribution centres or within large warehouses. Their ability to accurately and quickly deliver materials to the right place at the right time is invaluable, especially where there is a need to ensure the continuity of production processes.
AGVs can also be integrated into warehouse management systems (WMS), enabling automated inventory management and improved real-time tracking of material movements. This integration helps to optimise logistics processes and reduces the risk of errors when handling goods.
Sustainability and environmental benefits
Automated forklift trucks contribute to improving the company’s environmental profile. AGV systems are energy efficient and produce fewer emissions compared to traditional fossil fuel powered forklifts. Battery-powered AGVs also produce less noise, which contributes to better working conditions and reduces the negative impact on the surrounding environment.
Each AGV category has its own specific advantages and is designed for different applications. For example, while towing and underrun AGVs are ideal for material transport, fork lift AGVs are indispensable where loads need to be lifted and handled at height.
F1000AP: A breakthrough in the fork-lift AGV market
Among the market leaders in fork AGV manufacturers is Asseco CEIT, which has a wide portfolio of AGV equipment.
Asseco CEIT brings to the forked AGV segment a breakthrough innovation, the F1000AP, whose key advantage is in particular the extremely low handling space requirement, which is achieved by a revolutionary hidden fork system. This solution does not need supporting legs or counterbalance. The forks are part of the device itself, are fully extendable and thus allow the transport of material to reach a size that does not significantly exceed the size of the transport pallet itself. Material handling is possible both from the ground and from various static pedestals, allowing for versatile use.
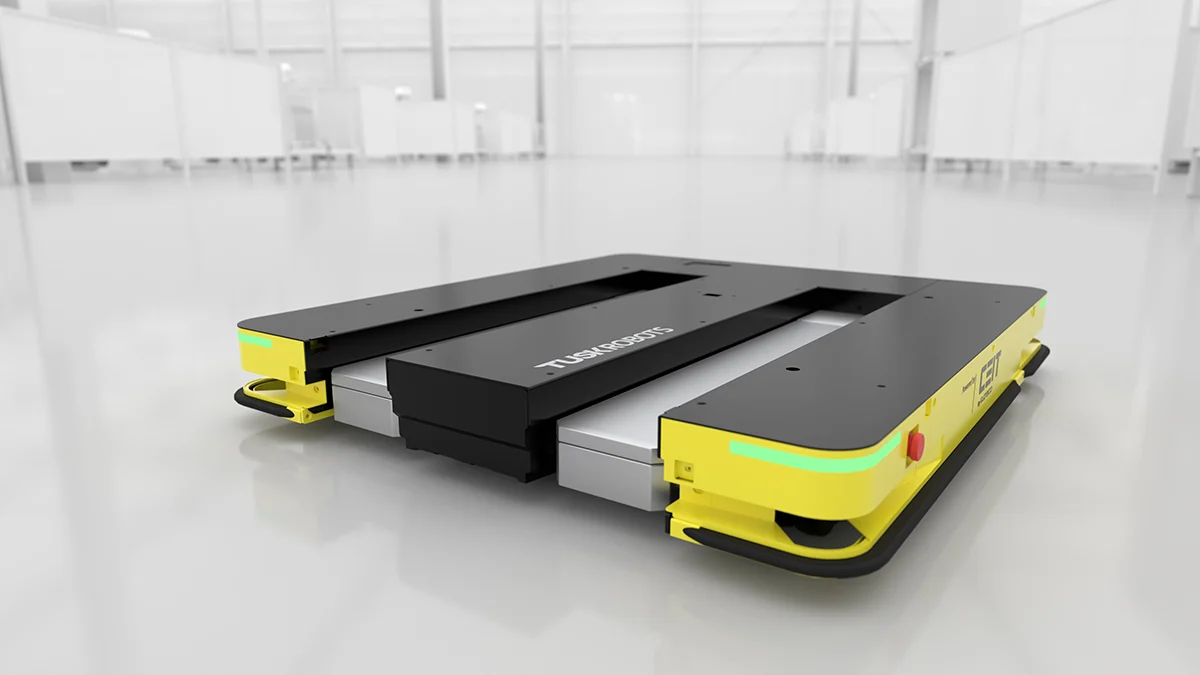
The AGV F1000AP is designed for material handling and transport in harsh industrial environments. This model uses advanced hybrid navigation systems that enable it to move accurately and safely and to provide perfect task repeatability. Thanks to advanced sensors and software solutions, the AGV can navigate even in complex spaces and automatically adjust its route according to the current conditions. These cutting-edge technologies allow it to operate with minimal human intervention.
One of the main benefits of the F1000AP is its continuous operation capability thanks to the continuous automatic charging system. Unlike traditional trucks that need breaks and maintenance, AGVs can operate continuously, which significantly increases productivity and return on investment. Its flexibility allows it to adapt to different working conditions and requirements, which is crucial in dynamic industrial environments.
With an advanced multi-dimensional safety system in the form of 360-degree laser area security, signal lights, audible alarm, safety STOP button and safety buffers, the F1000AP is a highly reliable solution for securing personnel, material and machinery and equipment in all kinds of operations.
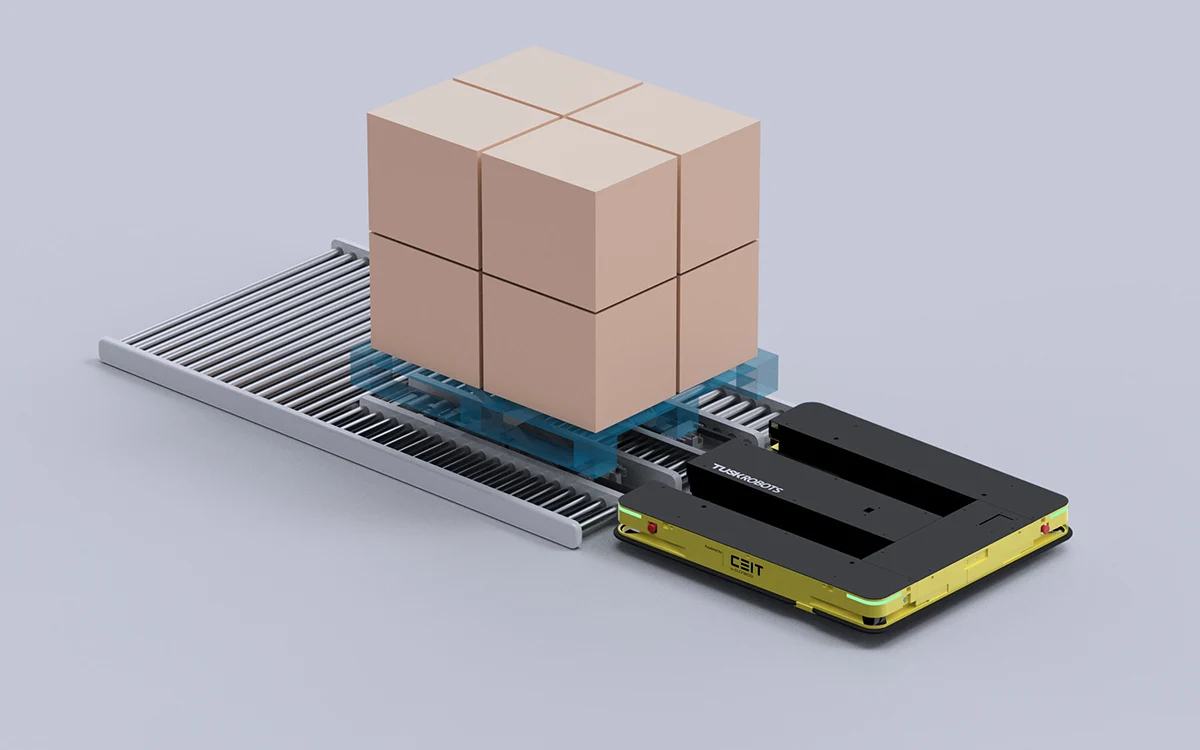

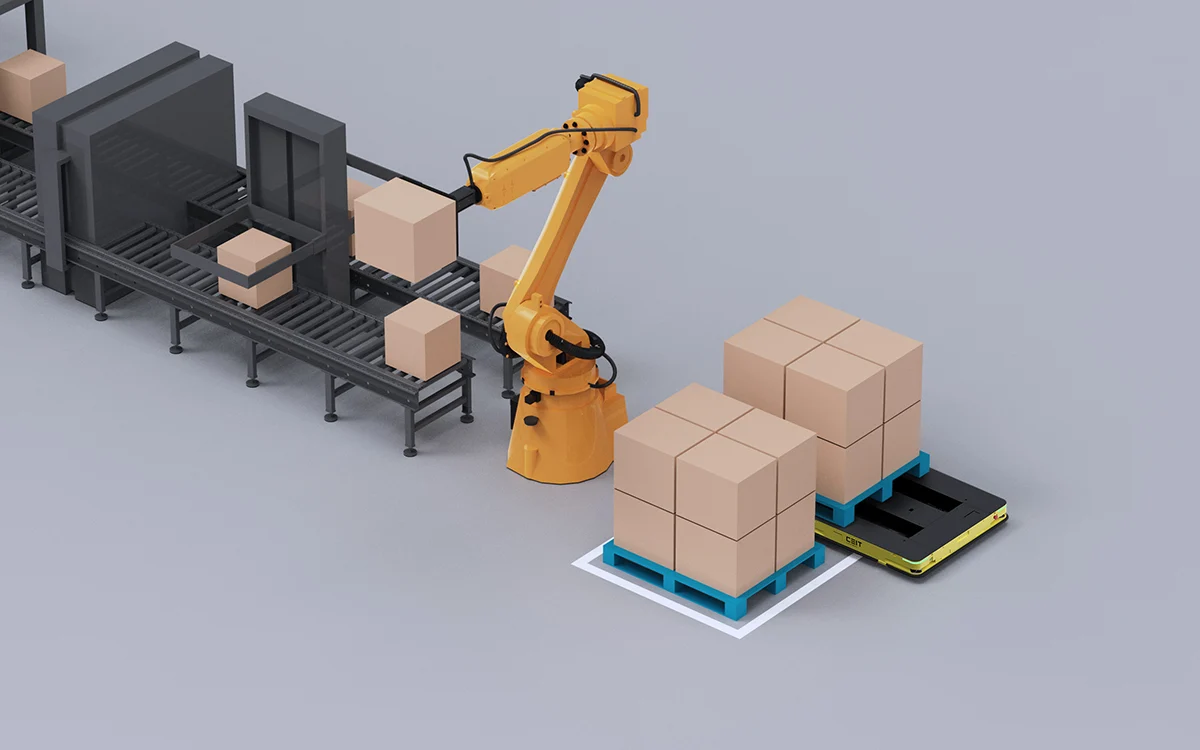
Future Prospects
AGV forklifts offer excellent scalability, allowing companies to grow and expand their operations without the need for major infrastructure changes. As a business grows, AGV systems can easily be expanded to include additional units or new features within a fully collaborative ecosystem, allowing them to keep pace with increasing demands.
The future of automated logistics technology is full of possibilities. With the development of artificial intelligence and advanced sensor technologies, AGV systems are expected to become increasingly autonomous and capable of performing even more complex tasks. Research and development in AGVs will bring further innovations that will improve their performance, safety and energy efficiency.